This article was written by our expert who is surveying the industry and constantly updating business plan for a transportation company.
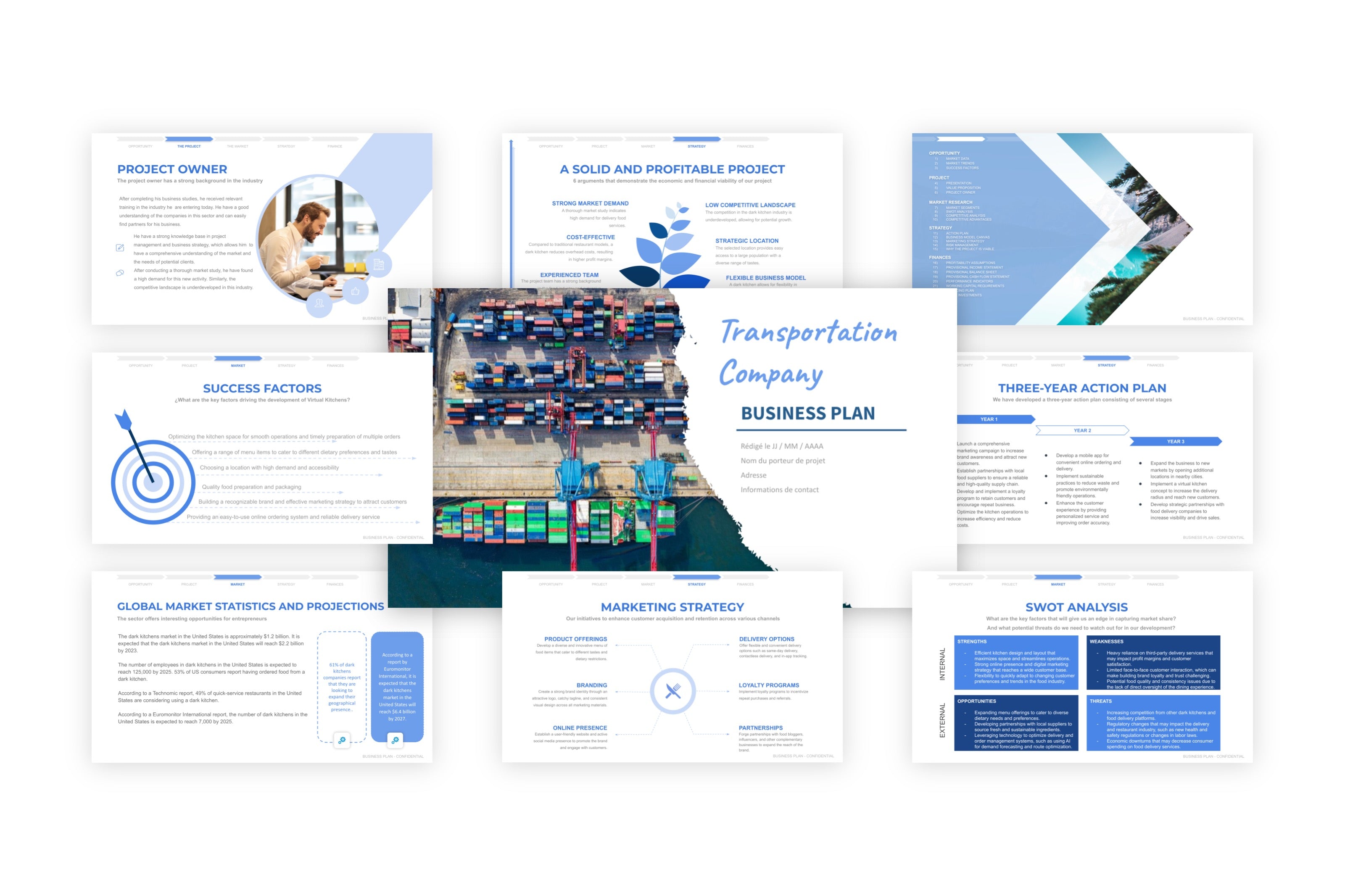
Our business plan for a transportation company will help you succeed in your project.
How many trucks and packing stations do you need to smoothly handle the busy seasons in your moving company without any hiccups?
How many trucks does a moving company need during busy seasons?
What's the best number of packing stations for a moving company when it's busy?
How much should a moving company set aside for extra trucks during busy times?
How much does demand for moving services go up during busy seasons?
How many extra staff should a moving company bring on for busy seasons?
How much more revenue can a moving company expect during busy seasons?
How long should a moving company prepare for busy season operations?
What's the usual truck usage rate during busy seasons?
How much should a moving company spend on marketing during busy seasons?
How far in advance do people usually book moving services during busy seasons?
How can a moving company keep fuel costs down during busy seasons?
What should a moving company think about when adding more trucks for busy seasons?
These are questions we frequently receive from entrepreneurs who have downloaded the business plan for a transportation company. We’re addressing them all here in this article. If anything isn’t clear or detailed enough, please don’t hesitate to reach out.
The Right Formula to Determine the Optimal Number of Trucks and Packing Stations for Peak Seasons
- 1. Analyze historical demand data:
Review past records to determine the number of moves during peak seasons. Identify patterns and trends to forecast future demand accurately.
- 2. Calculate the total number of moves:
Estimate the total number of moves expected during the peak season based on historical data and market trends.
- 3. Determine the average time per move:
Calculate the average time required for each move, including loading, transit, and unloading.
- 4. Calculate truck capacity:
Determine how many moves a single truck can handle per day, considering the average time per move and the length of the work shift.
- 5. Estimate the number of trucks needed:
Divide the total number of moves by the number of moves a single truck can handle over the peak season. Round up to ensure full coverage and account for unexpected delays or maintenance.
- 6. Calculate packing time requirements:
Estimate the total packing time needed by multiplying the number of moves by the average packing time per move.
- 7. Determine packing station capacity:
Calculate how many hours a single packing station can operate during the peak season, based on daily operating hours and the number of days in the peak season.
- 8. Estimate the number of packing stations needed:
Divide the total packing time required by the capacity of a single packing station. Round up to ensure efficiency and flexibility.
- 9. Finalize the number of trucks and packing stations:
Based on the calculations, determine the optimal number of trucks and packing stations needed to effectively manage peak season demand.
A Practical Example for Clarity
Adjust the bold numbers as needed and see how it works for your project.
To help you better understand, let’s take a fictional example. Imagine a moving company that operates in a mid-sized city and experiences peak demand during the summer months, specifically from June to August. During this period, the company estimates that it will need to handle 1,200 moves.
Each move requires an average of 4 hours, including loading, transit, and unloading time. The company operates 8-hour shifts, which means each truck can handle 2 moves per day. Therefore, over the 92 days of the peak season, a single truck can complete 184 moves (92 days x 2 moves per day).
To meet the demand of 1,200 moves, the company would need approximately 6.52 trucks (1,200 moves ÷ 184 moves per truck), which rounds up to 7 trucks to ensure full coverage and account for any unexpected delays or maintenance issues.
Next, consider the packing stations. Assume that each move requires 2 hours of packing time, and each packing station can handle one move at a time. With 1,200 moves and 2 hours of packing per move, the company needs 2,400 hours of packing time.
If the company operates packing stations for 8 hours a day over the 92-day peak season, each station can provide 736 hours of packing time (92 days x 8 hours). To meet the total packing demand, the company would need approximately 3.26 packing stations (2,400 hours ÷ 736 hours per station), which rounds up to 4 packing stations to ensure efficiency and flexibility.
In conclusion, for the peak moving season, the company should have 7 trucks and 4 packing stations to effectively manage the demand and maintain smooth operations.

With our financial plan for a transportation company, you will get all the figures and statistics related to this industry.
Frequently Asked Questions
- How do I calculate the revenue needed per trip to cover costs in my transportation company?
- A free example of business plan for a fish market
- Starting a transportation company: the step-by-step guide
How many trucks should a moving company have for peak seasons?
A moving company should aim to have between 10 and 20 trucks to handle peak season demand effectively.
This number can vary based on the size of the market and the company's service area.
It's crucial to analyze past data and forecast future demand to determine the optimal fleet size.
What is the ideal number of packing stations for a moving company during peak times?
For peak seasons, a moving company should have at least 5 to 10 packing stations to ensure efficiency.
The number of stations depends on the volume of moves and the complexity of packing requirements.
Having enough packing stations helps in reducing bottlenecks and improving customer satisfaction.
How much should a moving company budget for additional trucks during peak seasons?
A moving company should budget between $50,000 and $100,000 per truck for additional vehicles during peak seasons.
This includes costs for leasing or purchasing, as well as maintenance and insurance.
Proper budgeting ensures that the company can meet demand without financial strain.
What is the expected increase in demand for moving services during peak seasons?
Demand for moving services can increase by up to 50% during peak seasons.
This surge requires careful planning and resource allocation to meet customer needs.
Understanding seasonal trends helps a transportation company prepare adequately.
How many additional staff members should a moving company hire for peak seasons?
A moving company may need to hire between 20% and 30% more staff during peak seasons.
This includes drivers, packers, and administrative support to handle increased workloads.
Temporary staffing solutions can be a cost-effective way to manage seasonal demand.
What is the average revenue increase for a moving company during peak seasons?
A moving company can expect a revenue increase of between 30% and 50% during peak seasons.
This boost is due to higher demand and potentially higher rates for services.
Maximizing efficiency and customer satisfaction can further enhance revenue growth.
How long should a moving company plan for peak season operations?
Peak season operations typically last between 3 and 4 months for a moving company.
This period often includes summer months and the end of the year when moving activity is highest.
Proper planning ensures that resources are available throughout the entire peak period.
What is the typical utilization rate of trucks during peak seasons?
During peak seasons, a moving company's trucks can have a utilization rate of up to 90%.
High utilization rates indicate efficient use of resources and increased profitability.
Monitoring utilization helps in making informed decisions about fleet expansion.
How much should a moving company invest in marketing for peak seasons?
A moving company should allocate between 5% and 10% of projected peak season revenue to marketing efforts.
Effective marketing can help capture a larger share of the increased demand during peak times.
Investing in targeted campaigns can enhance brand visibility and customer acquisition.
What is the average lead time for booking moving services during peak seasons?
During peak seasons, customers typically book moving services 4 to 6 weeks in advance.
Understanding lead times helps a transportation company manage schedules and resources effectively.
Encouraging early bookings can help in planning and optimizing operations.
How should a moving company manage fuel costs during peak seasons?
A moving company should implement fuel-efficient practices to manage costs during peak seasons.
This includes route optimization, regular vehicle maintenance, and driver training.
Monitoring fuel consumption helps in identifying areas for cost savings and efficiency improvements.
What are the key factors to consider when expanding a moving company's fleet for peak seasons?
Key factors include market demand, financial capacity, and operational efficiency.
It's important to assess whether the current infrastructure can support additional vehicles.
Strategic planning ensures that fleet expansion aligns with business goals and customer needs.